工厂生产管理系统软件费用标准
模具行业是一个技术密集、资金密集、劳动力密集的行业,其特点包括产品种类繁多、生产周期长、工艺复杂、质量要求高等。这些特点使得模具行业在生产管理上面临着诸多挑战,如生产计划难以安排、物料管理混乱、工艺流程复杂、质量控制困难等。因此,引入生产管理软件,对于解决这些问题具有重要意义。生产管理软件是一种集成了生产计划、物料管理、工艺流程、质量管理等多个功能模块的软件系统。它通过对生产过程中的各种数据进行收集、分析和处理,帮助企业实现生产过程的自动化、智能化管理。生产管理软件的应用,不仅可以提高生产效率和产品质量,还可以降低生产成本,增强企业的市场竞争力。电子行业生产管理系统的可集成性使得可以轻松整合各种现有系统和设备,实现企业信息系统的高效协同。工厂生产管理系统软件费用标准
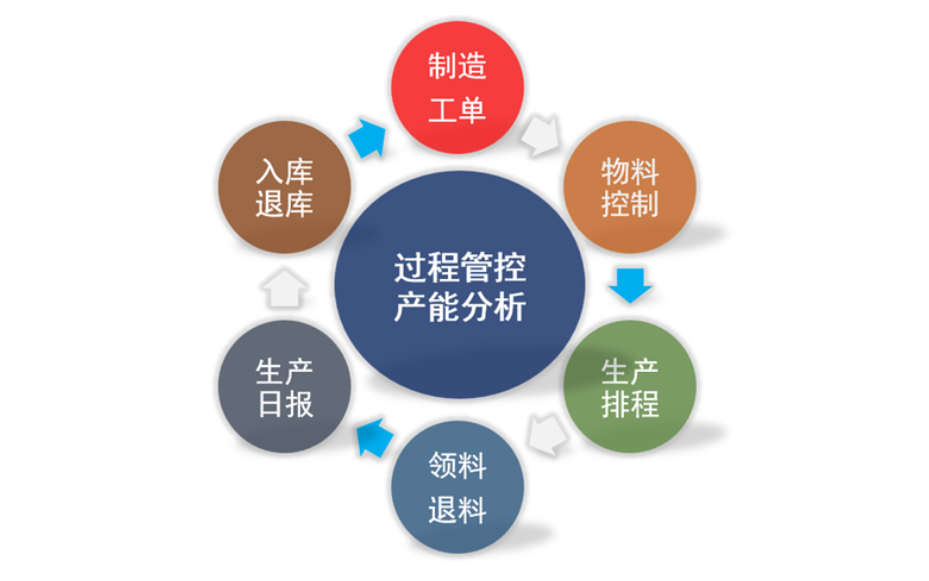
生产管理软件通过自动化和智能化的管理方式,有效减轻了管理人员的工作负担。软件能够自动完成生产计划制定、物料采购、生产进度跟踪等繁琐任务,使管理人员有更多的时间和精力用于分析和解决生产过程中的问题。同时,软件还能提供丰富的报表和图表功能,帮助管理人员直观地了解生产状况和经营成果,提高管理效率。生产管理软件作为一个统一的平台,能够将生产、采购、销售、财务等各个部门紧密地联系在一起。通过软件平台,各部门之间可以实时共享生产数据和信息,加强沟通和协作,共同推动生产任务的完成。这种跨部门协作的方式有助于打破部门壁垒,形成合力,提高企业的整体运营效率。浙江小型工厂生产管理软件在模具行业,生产管理软件帮助企业实现了供应链的有效整合,提高了供应链的响应速度。
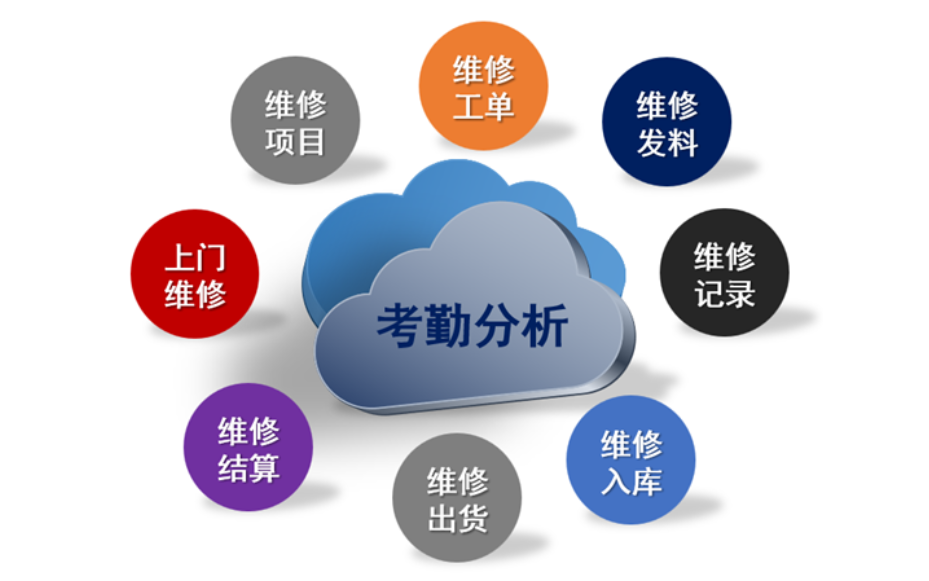
塑胶行业的生产过程中涉及大量的原材料和成品库存,如何有效管理和优化库存成为企业的重要课题。生产管理软件可以通过实时监控和分析库存数据,帮助企业实现库存的精细化管理和优化。软件可以根据订单和销售预测等信息,自动计算和调整库存水平,避免库存过高或过低的情况发生。同时,软件还可以优化物流配送和运输路线,提高物流效率和降低物流成本。塑胶行业的生产设备通常需要进行定期的维护和保养,以确保其正常运行和延长使用寿命。生产管理软件可以帮助企业实现设备维护的计划和管理。软件可以根据设备的使用情况和维护记录,提供维护计划和提醒,确保设备的正常运行和维护工作的及时进行。此外,软件还可以监控和分析设备的能源消耗情况,帮助企业实现能源的节约和管理,降低生产成本和环境影响。
生产管理软件在模具行业的优势有:1、提高生产效率:通过生产管理软件的自动化、智能化管理,可以有效减少人工干预和误差,提高生产效率。同时,软件系统还可以对生产过程进行实时监控和调整,确保生产过程的稳定性和连续性。2、降低成本:生产管理软件可以帮助企业优化资源配置、减少浪费、降低库存成本等,通过软件系统的数据分析功能,还可以帮助企业发现潜在的成本节约点,进一步提高成本控制能力。3、提高产品质量:通过生产管理软件的质量管理体系建立和质量数据收集分析功能,可以及时发现和解决质量问题,提高产品质量水平。同时,软件系统还可以提供质量追溯功能,增强产品的可追溯性和可控制性。在模具行业,生产管理软件帮助企业实现了从接单到交货的全流程跟踪管理。
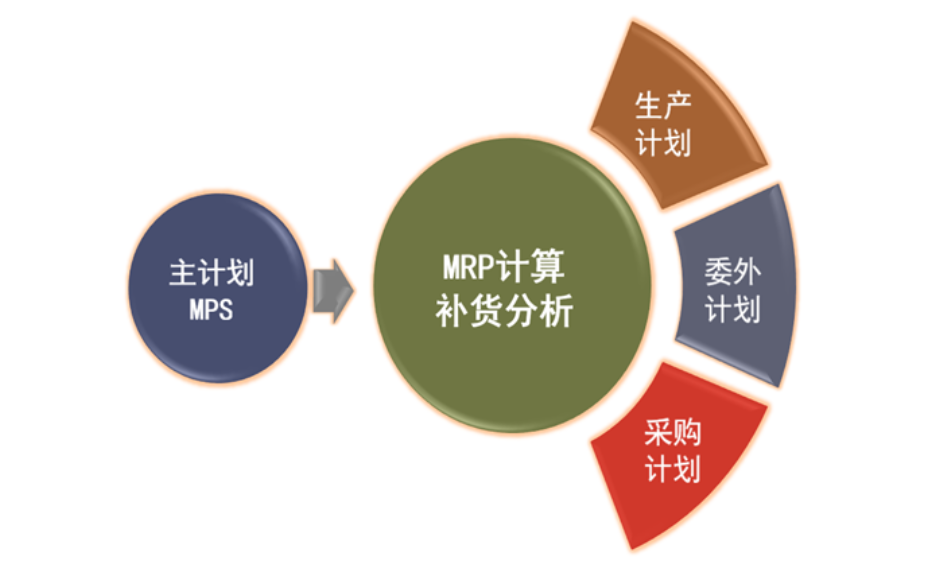
生产管理软件通过集成生产计划、物料需求计划、能力需求计划等功能,实现对生产过程的控制。软件可以根据订单需求、库存情况、设备状态等因素,自动生成生产计划,并实时调整生产进度。同时,软件还可以对生产设备进行调度,确保设备的高效运行和资源的合理利用。塑胶行业的原材料种类繁多,物料管理是一项繁琐而重要的工作。生产管理软件通过物料编码、库存预警、物料追溯等功能,实现对原材料的精细化管理。软件可以实时记录原材料的入库、出库、库存等信息,为企业的采购、生产和销售提供准确的数据支持。同时,软件还可以对物料的使用情况进行跟踪和分析,帮助企业优化物料使用,降低成本。离散制造行业生产管理系统是一种高效的生产管理模式,有助于提高生产效率和产品质量。生产管理软件收费明细
模具行业生产管理系统支持对设备的维护和管理,能够提高设备的利用率和寿命。工厂生产管理系统软件费用标准
模具行业的库存管理一直是一个难题,过高的库存会增加企业的资金压力,而过低的库存则可能导致生产中断。生产管理软件可以通过对销售预测、生产计划和库存数据的分析,帮助企业实现库存管理的优化。软件可以自动计算库存水平,并提供及时的库存报警和补货建议,避免库存过高或过低的情况发生,提高资金利用效率。生产管理软件可以实现生产过程的可视化管理,通过数据采集和监控设备的连接,实时显示生产线上的各项指标和状态。这样,企业管理人员可以随时了解生产情况,及时发现问题并采取措施,提高生产线的稳定性和可靠性。工厂生产管理系统软件费用标准
上一篇: 模具行业生产管理业务咨询
下一篇: 小型服装生产管理系统价钱