轴类零件加工中心推荐
滚削加工和磨削加工有什么区别?滚削加工和磨削加工是常用的两种精密加工方法,它们有以下几个主要区别:1. 加工原理:滚削加工是利用刀具(滚刀)在工件上进行旋转切削,将工件上的材料切削掉来达到加工的目的;磨削加工则是利用磨粒对工件表面进行磨削,通过磨粒与工件间的磨擦来去除材料并形成所需的形状。2. 切削方式:滚削加工是连续的切削过程,切屑呈螺旋状从工件上排除;而磨削加工是间歇的磨削过程,磨粒在工件表面滚动磨擦产生高温而去除材料。3. 精度和表面质量:滚削加工由于刀具刃口的几何形状和较小的切削宽度,通常能够实现较高的加工精度和较好的表面质量;而磨削加工则可以进一步提高精度和表面质量,因为磨削过程能够更好地消除工件上的微小凹陷和瑕疵。4. 加工效率:滚削加工相对于磨削加工通常具有更高的加工效率,因为滚削加工可以实现较大的切削速度和进给速度,适用于大批量生产和高效加工的需求。磨削加工中心采用磨削工艺,能够实现很高的加工精度。轴类零件加工中心推荐
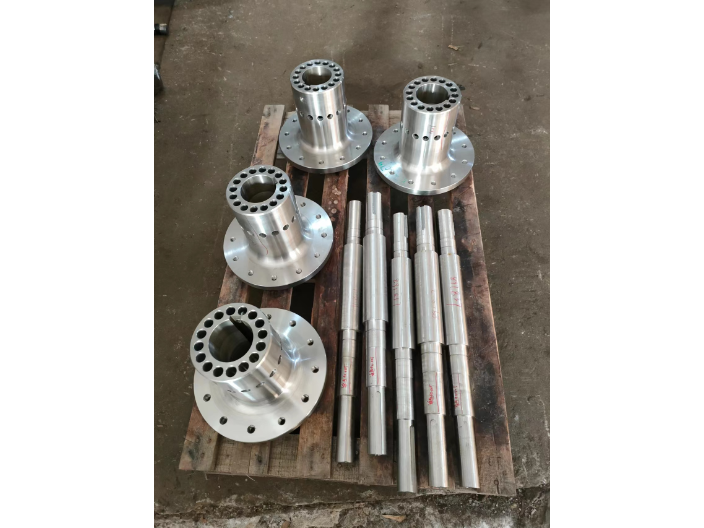
滚削加工过程中需要注意什么?滚削加工是一种常用的金属加工方法,可以用于制造各种零部件。在进行滚削加工时,需要注意以下几点:1. 工件固定:确保工件在滚削过程中的稳定固定,避免工件晃动、移位或夹持不牢。选择适当的夹具和夹持方式,保证工件与滚轮之间的正确配合。2. 选用合适的滚轮:根据被加工工件的材料和形状选择合适的滚轮。滚轮的材料和硬度应与工件相匹配,并具有足够的耐磨性和刚性以确保加工质量。3. 控制滚削参数:合理设置滚削参数,包括进给速度、转速和切削深度等。这些参数的选择应根据工件的要求和材料特性进行调整,以保证加工效率和表面质量。4. 冷却润滑:在滚削加工过程中,应使用适当的冷却液或润滑液来降低摩擦和磨损,并有效排除加工产生的热量。同时,冷却液还能清洗切屑和保护工具表面,提高加工质量和工具寿命。轴类零件加工中心推荐滚削加工可以减少切削力的突变,减小切削过程中的冲击和表面热影响区域,增加了加工的稳定性。
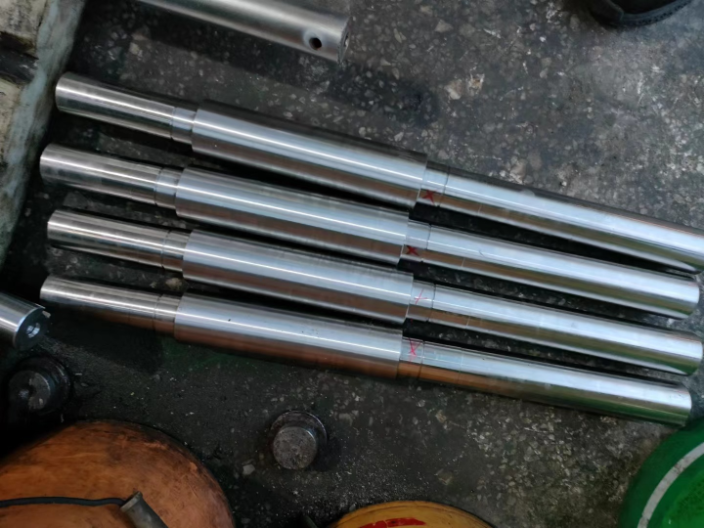
如何选择磨削加工中心呢?在选择磨削加工中心时,可以考虑以下几个因素:1. 加工需求:首先确定您的加工需求,包括要加工的零件材料、形状、尺寸和精度要求等。不同的磨削加工中心具有不同的功能和加工能力,需要根据需求选择适合的型号和规格。2. 精度要求:磨削加工中心的精度是非常重要的考虑因素之一。根据您的零件精度要求,选择具备高精度控制系统和稳定性的磨削加工中心,并确保其能够满足您的加工精度要求。3. 加工能力:考虑磨削加工中心的加工能力,包括最大加工尺寸、加工速度和加工精度等。确保选购的设备能够满足您的加工需求,并具备足够的加工范围和高效的加工能力。
螺纹轴铣削加工是一种常见的加工过程,用于制造具有螺纹结构的零件。以下是螺纹轴铣削加工的一些工艺特点:1. 工艺复杂:螺纹轴铣削加工需要考虑螺纹的形状、尺寸、螺距等因素,需要合理选择切削参数和工艺路径。2. 刀具选择:合适的刀具是确保加工质量和效率的关键。一般使用螺纹铣刀、插齿刀或者螺纹铣刀与插齿刀的组合刀具。3. 加工工艺参数设定:包括进给速度、转速、切削深度等参数的选择。根据螺纹的要求,选择合适的参数以保证加工质量和工件表面粗糙度。4. 夹具设计:夹具对于螺纹轴铣削加工非常重要。夹具必须能够稳定固定工件,同时允许切削刀具进入和退出,以确保加工精度和安全性。5. 安全操作:螺纹轴铣削加工需要注意安全操作。操作人员应熟悉加工机床的操作规程和注意事项,佩戴必要的防护装备,并遵循安全操作规程。螺纹轴铣削加工可以同时完成多个螺纹的加工,提高了加工效率。
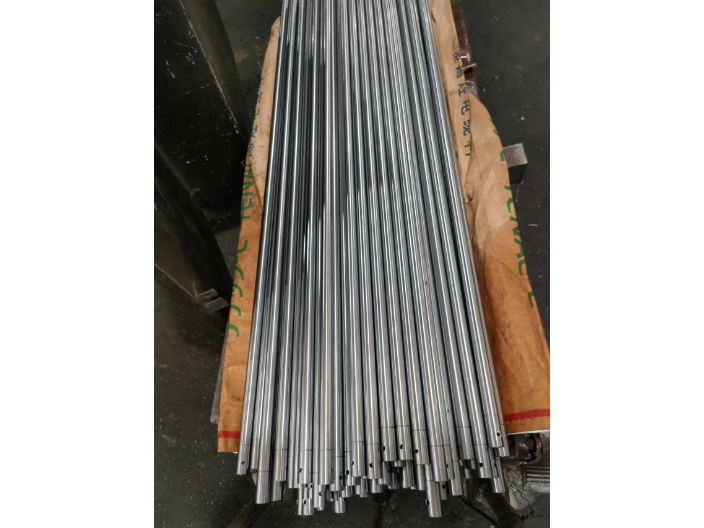
轴类零件滚削加工的注意事项有哪些?在进行轴类零件滚削加工时,有一些注意事项需要注意。以下是一些常见的注意事项:1. 选择适当的刀具和切削参数:根据不同材料和工件性质,选择合适的切削刀具和切削参数,包括切削速度、进给速度、切削深度等。这样可以确保加工过程稳定、高效,并获得良好的加工质量。2. 使用合适的冷却液:通过使用冷却液来冷却切削区域,可以有效降低摩擦和热量,减少刀具磨损,并避免工件变形。选择适合材料和加工过程的冷却液,并确保其充分润湿切削区域。3. 控制切削力和振动:高速旋转刀具在切削过程中会产生振动和切削力,因此需要采取措施来控制它们。合理选择刀具和切削参数,保持稳定的刀具刚度和切削深度,并采取有效的机械结构和固定方式,以减少振动和切削力的影响。选择轴类零件加工的好处是什么?轴类零件加工中心推荐
钻削加工是利用钻孔刀具进行直径加工的方法。轴类零件加工中心推荐
轴套加工完成后,需要进行质量检验和测试来确保产品达到要求。以下是一些常见的轴套质量检验和测试方法:1. 外观检查:对轴套的外观进行检查,包括表面光洁度、无裂纹、无毛刺等方面,确保产品外观符合要求。2. 尺寸测量:使用精密测量工具如千分尺、游标卡尺、显微镜等测量轴套的关键尺寸,与设计图纸进行比对,确定尺寸是否符合要求。3. 强度和硬度测试:根据轴套材料的不同,在合适的实验设备上进行强度和硬度测试,以确保轴套的材料性能满足要求。4. 表面粗糙度测试:使用表面粗糙度仪或投影仪等设备对轴套的表面粗糙度进行测量,确认其表面质量是否符合要求。5. 材料成分分析:通过化学分析测试仪器对轴套材料进行成分分析,确保使用的材料符合要求。6. 轴线偏直度和圆度检测:使用测量设备如高精度测螺旋仪等,测量轴套的轴线偏直度和圆度,确保其与设计要求相符。7. 装配测试:将轴套装配至要求的机械设备中,检查其在实际使用过程中的适配性和运行情况,确保轴套能够正常工作。8. 相关性能测试:根据具体应用需求,进行一些特定的测试,如耐磨性、耐腐蚀性、密封性等方面的测试,以验证轴套的相关性能。轴类零件加工中心推荐
上一篇: 河南铸铁车床加工哪家好
下一篇: 中空轴磨削加工中心推荐